Step 1: First of all we need to maintain QM data for the material master using MM02 transaction code.
Inspection Type 1701 stands for the Quality Inspection during GR from external vendor when using EWM.
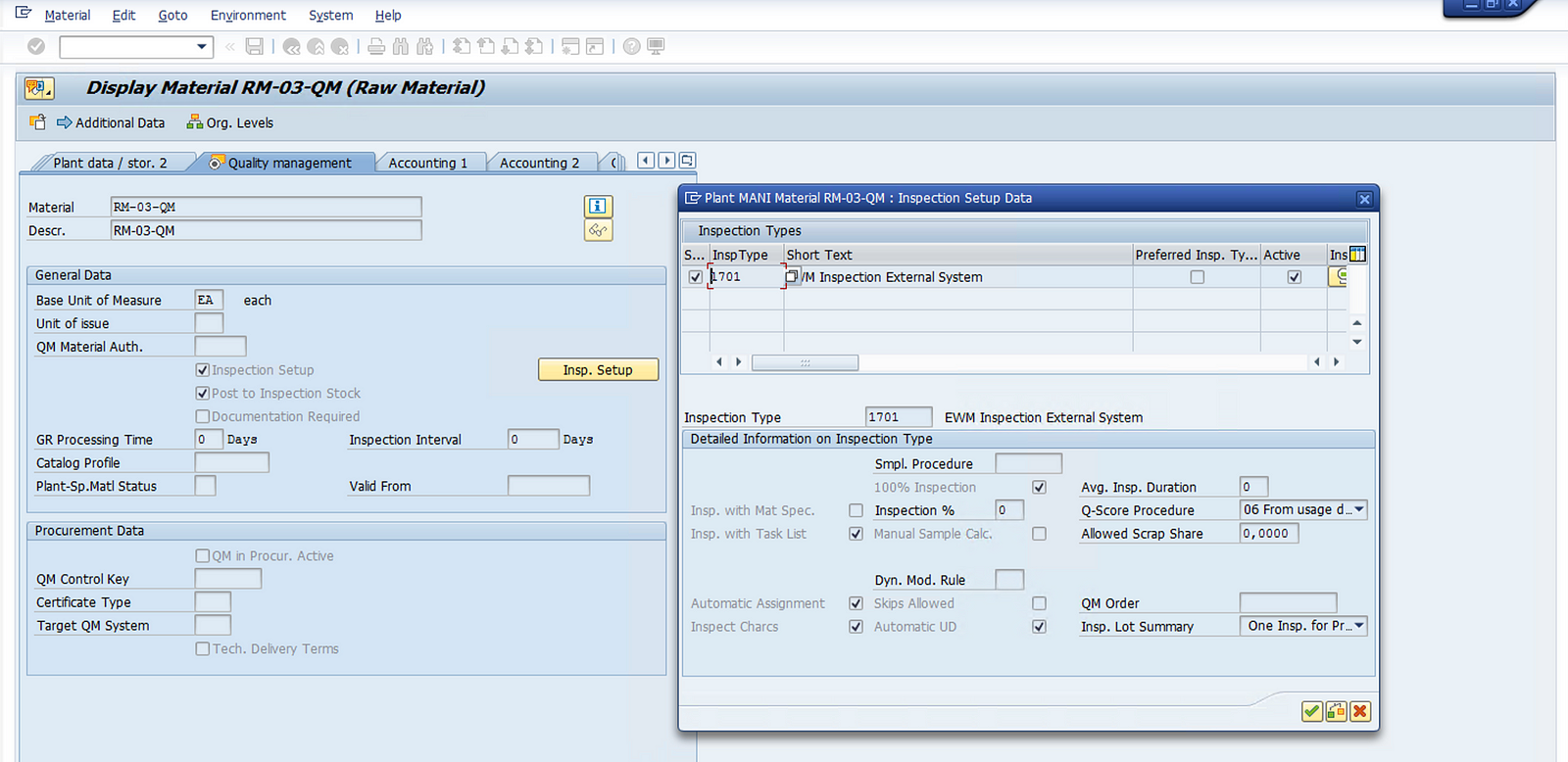
Step 2: Define and Maintain POSC for our EWM Warehouse. The POSC will have quality step as one of the steps during Putaway.
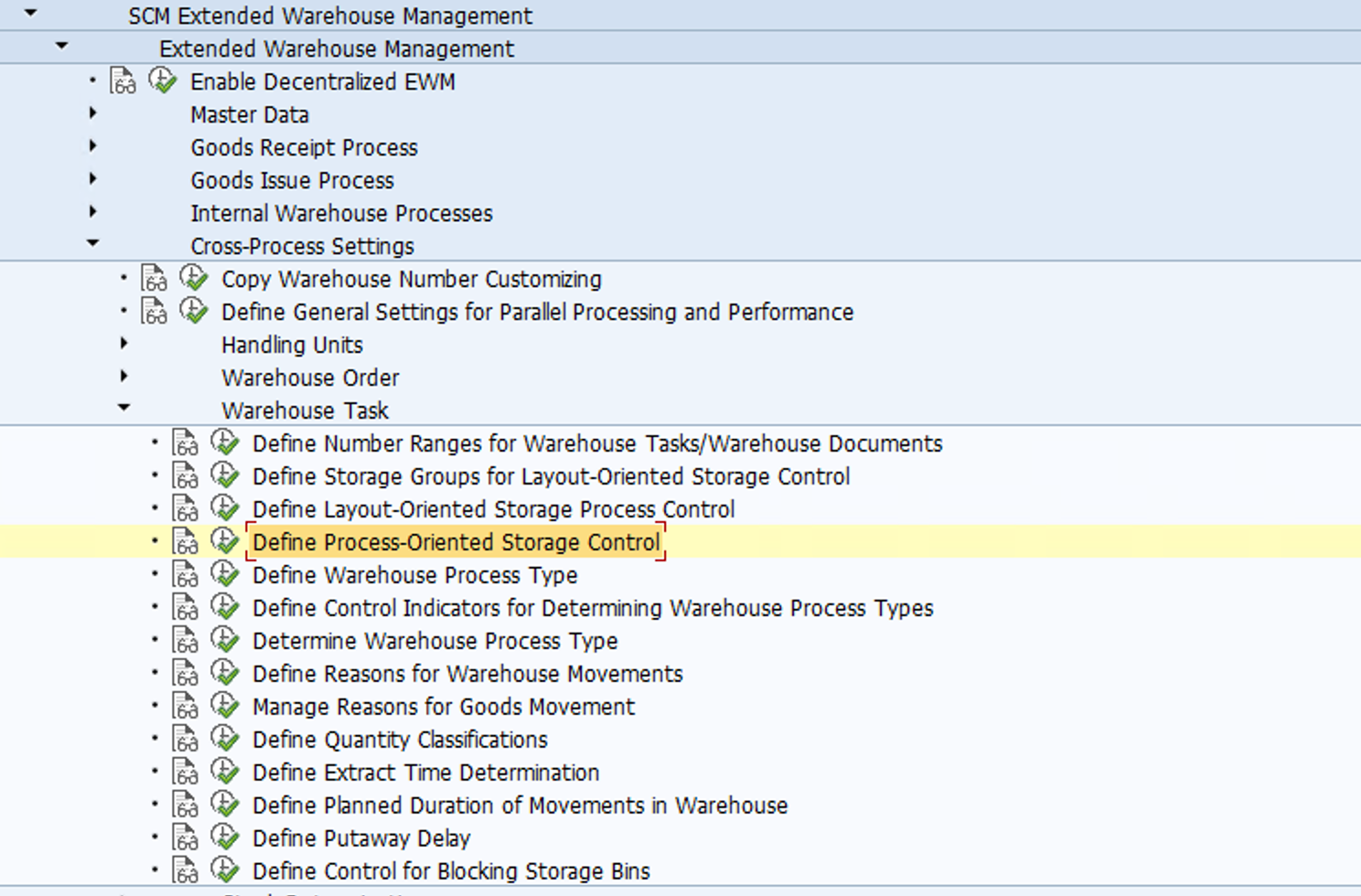
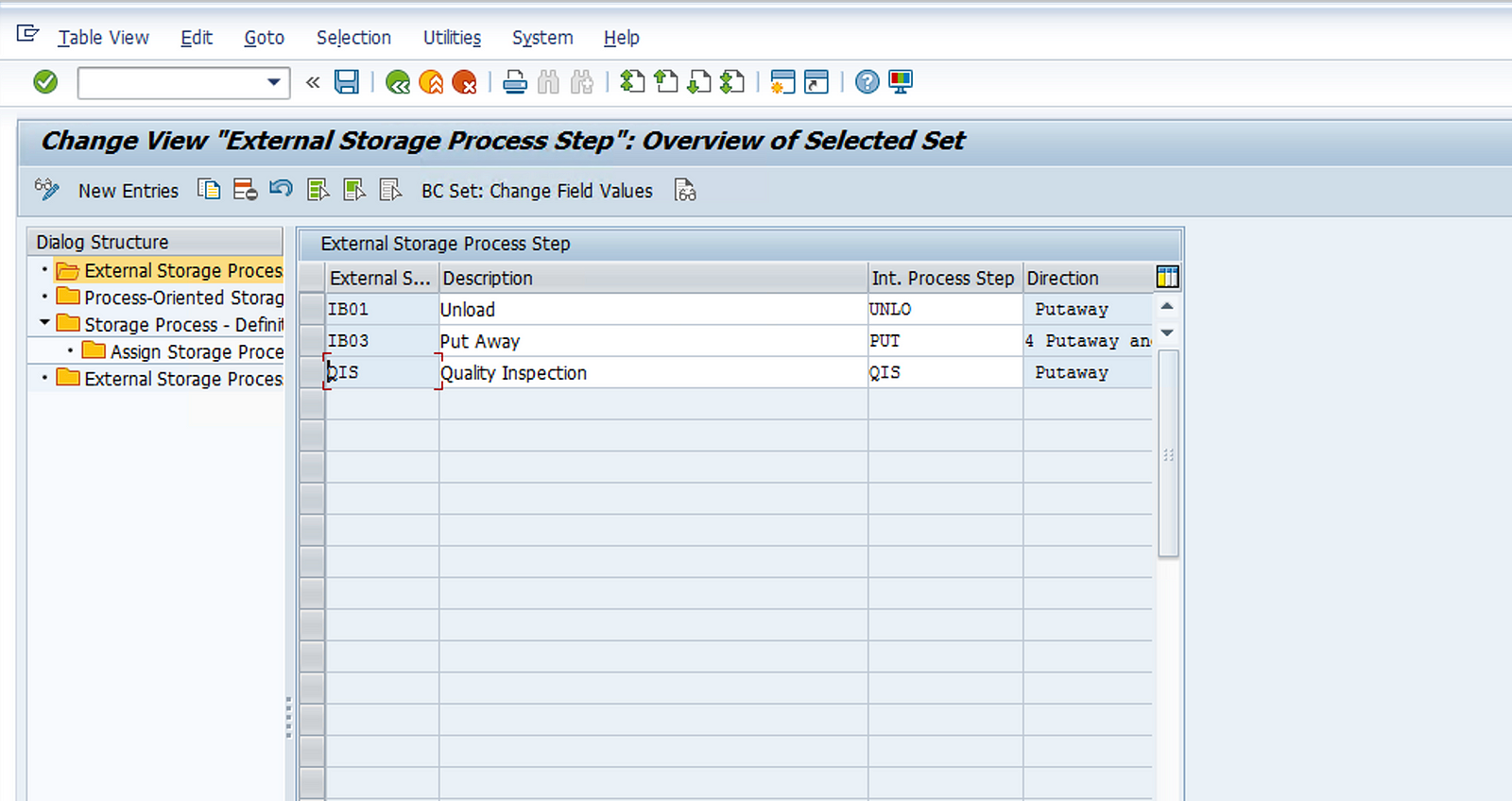
We also need to maintain below settings, to create WPTs please refer to this Blog. Also create the Storage type 9030 and 8020 if not already created. Create the Bin using tcode /SCWM/LS01
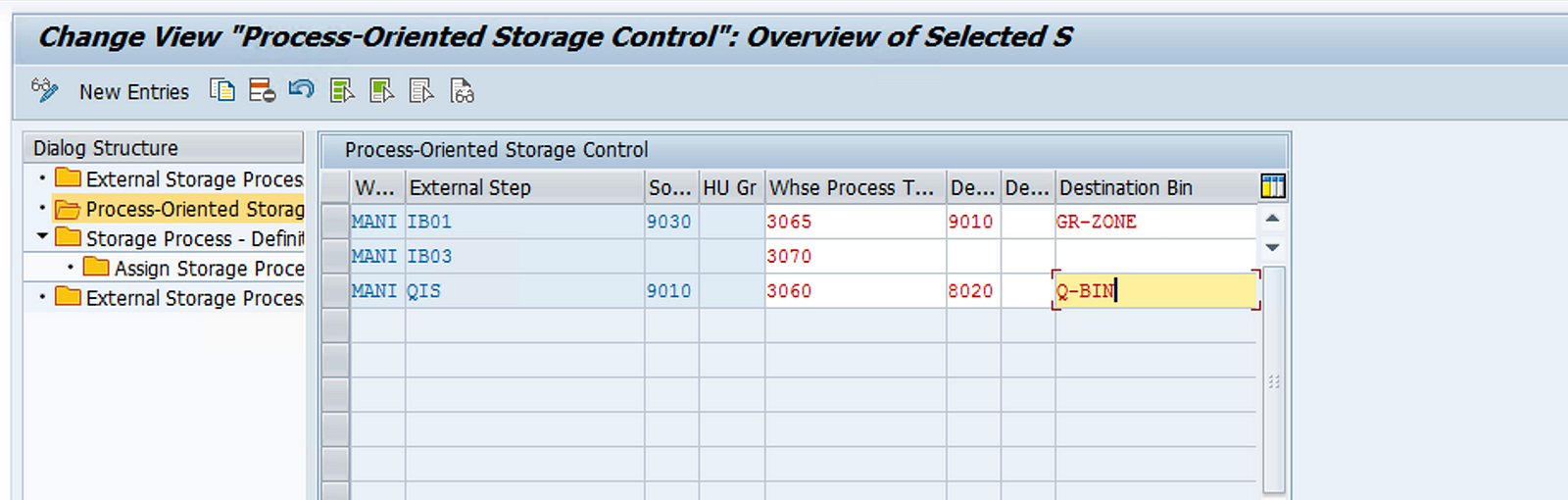
Define a storage process and assign the external steps to the storage process maintained for your warehouse.
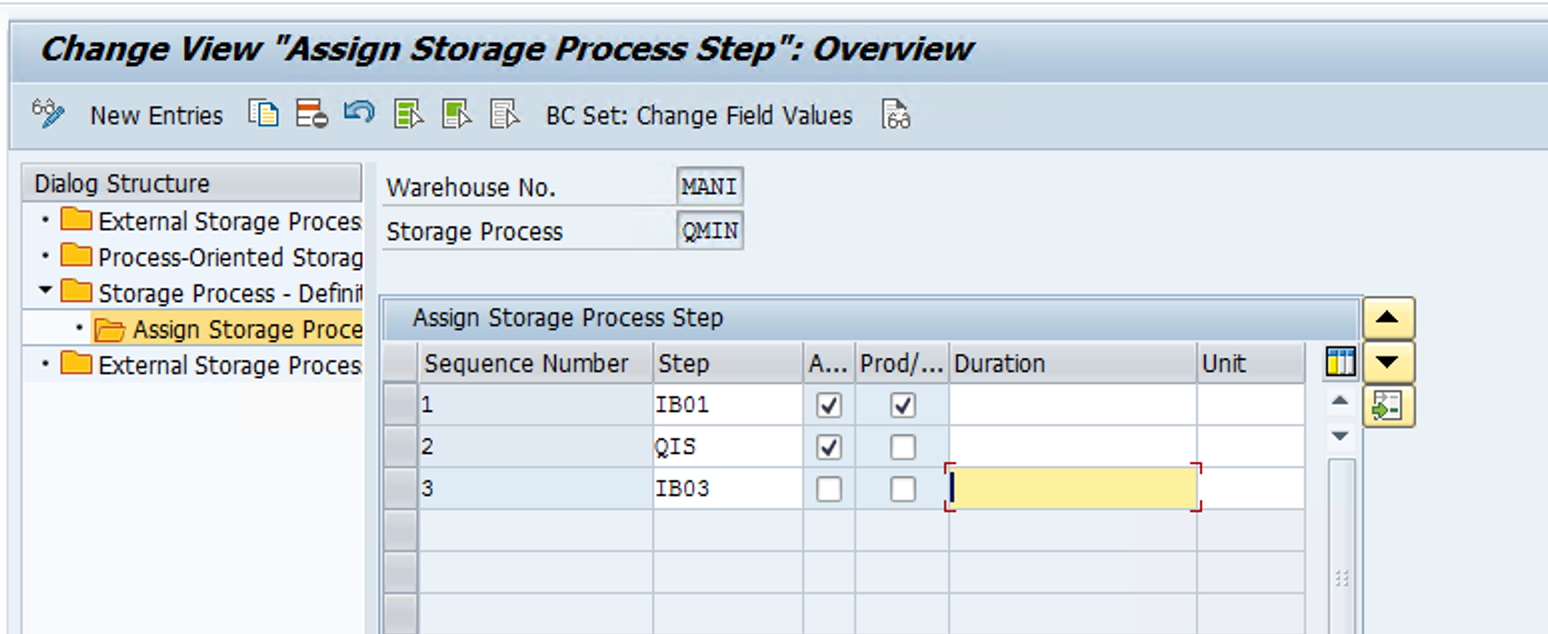
Step 3: Now we need to assign this to the WPT which will be used for Quality inspection process, we are creating WPT 1011 for quality purpose and assigning the POSC to the same.
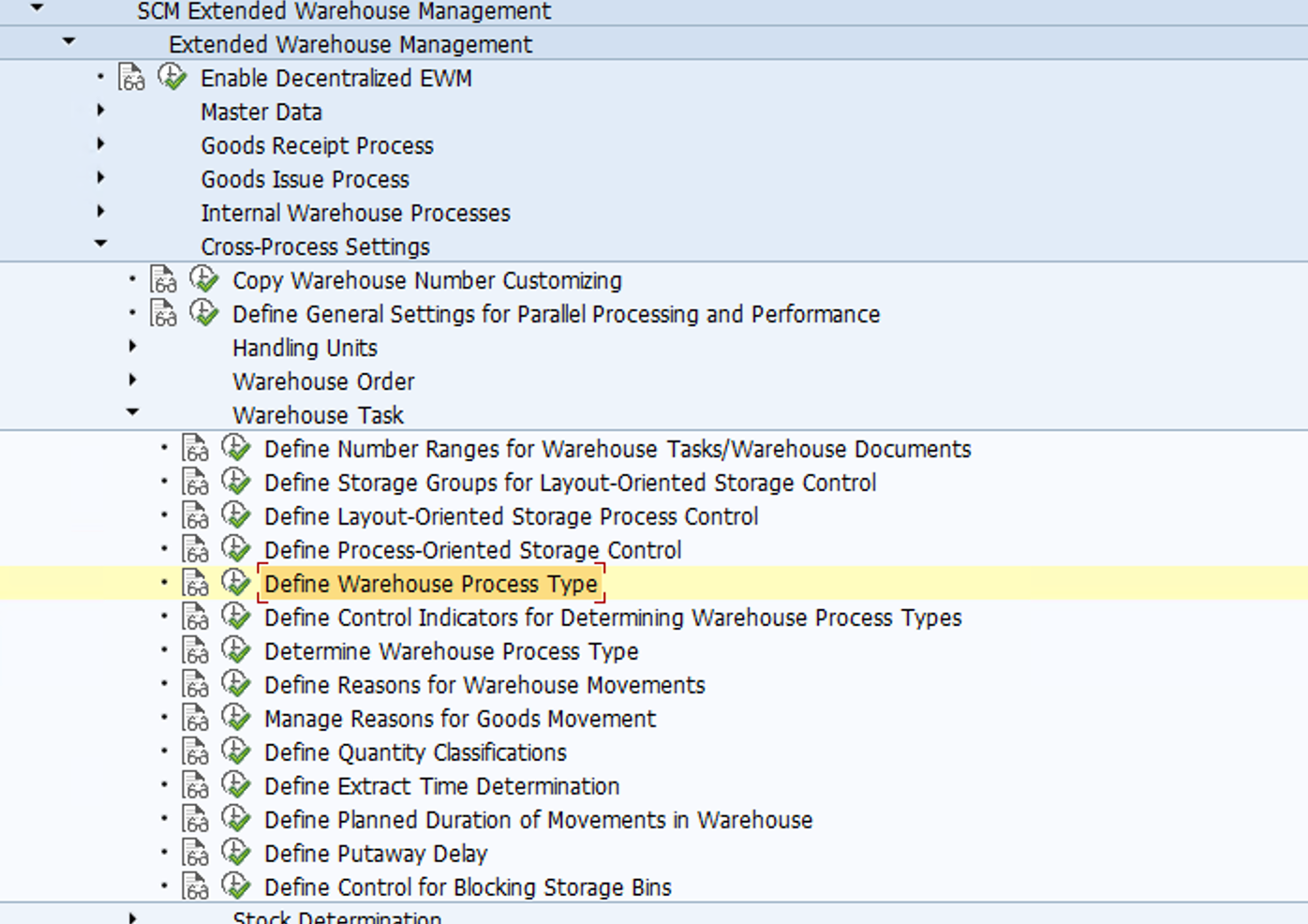
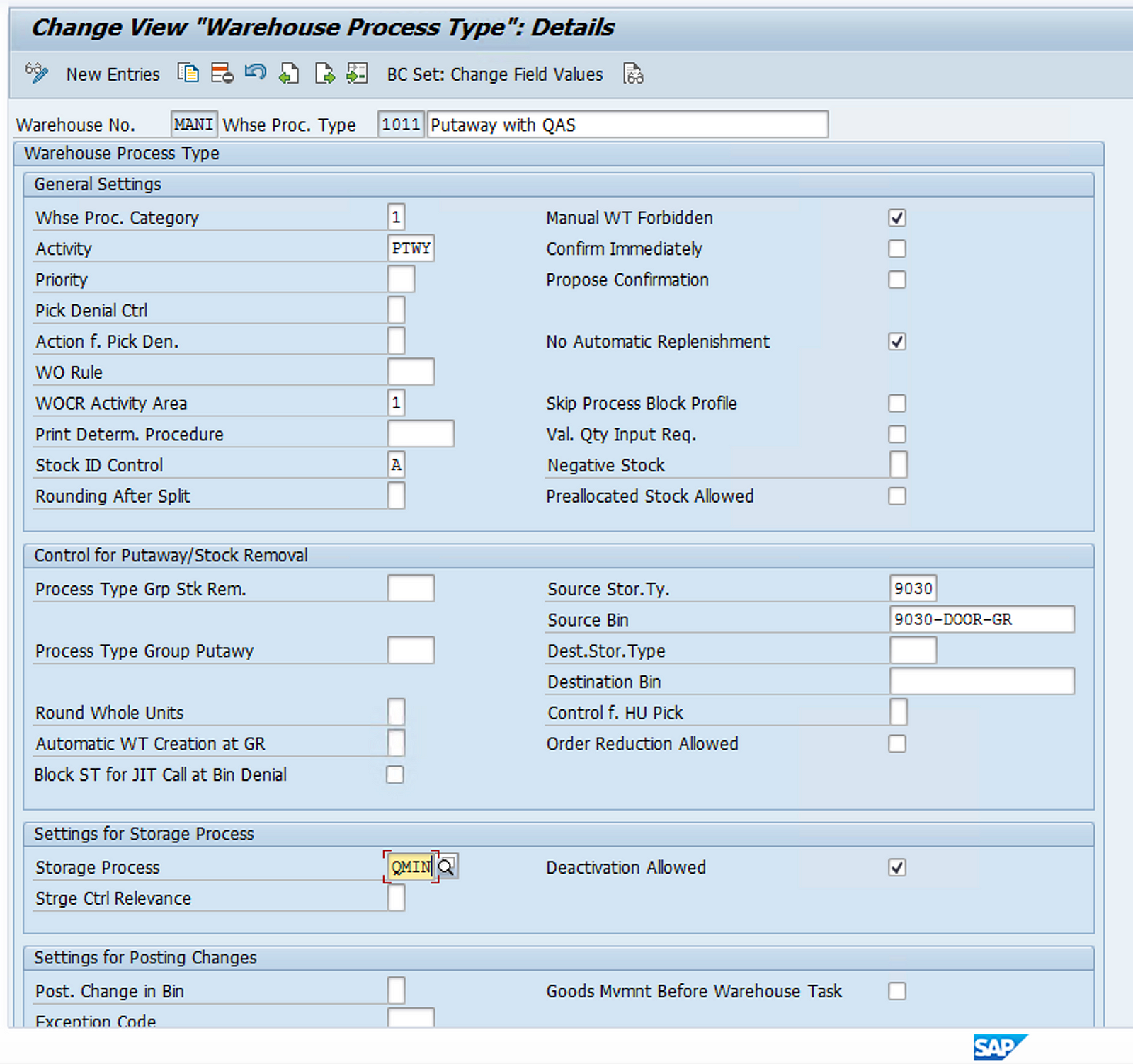
Step 4: Now we need to create the WPT indicator and quality inspection group and assign it to the product master so that POSC can get triggered when Inbound is processed in the EWM.
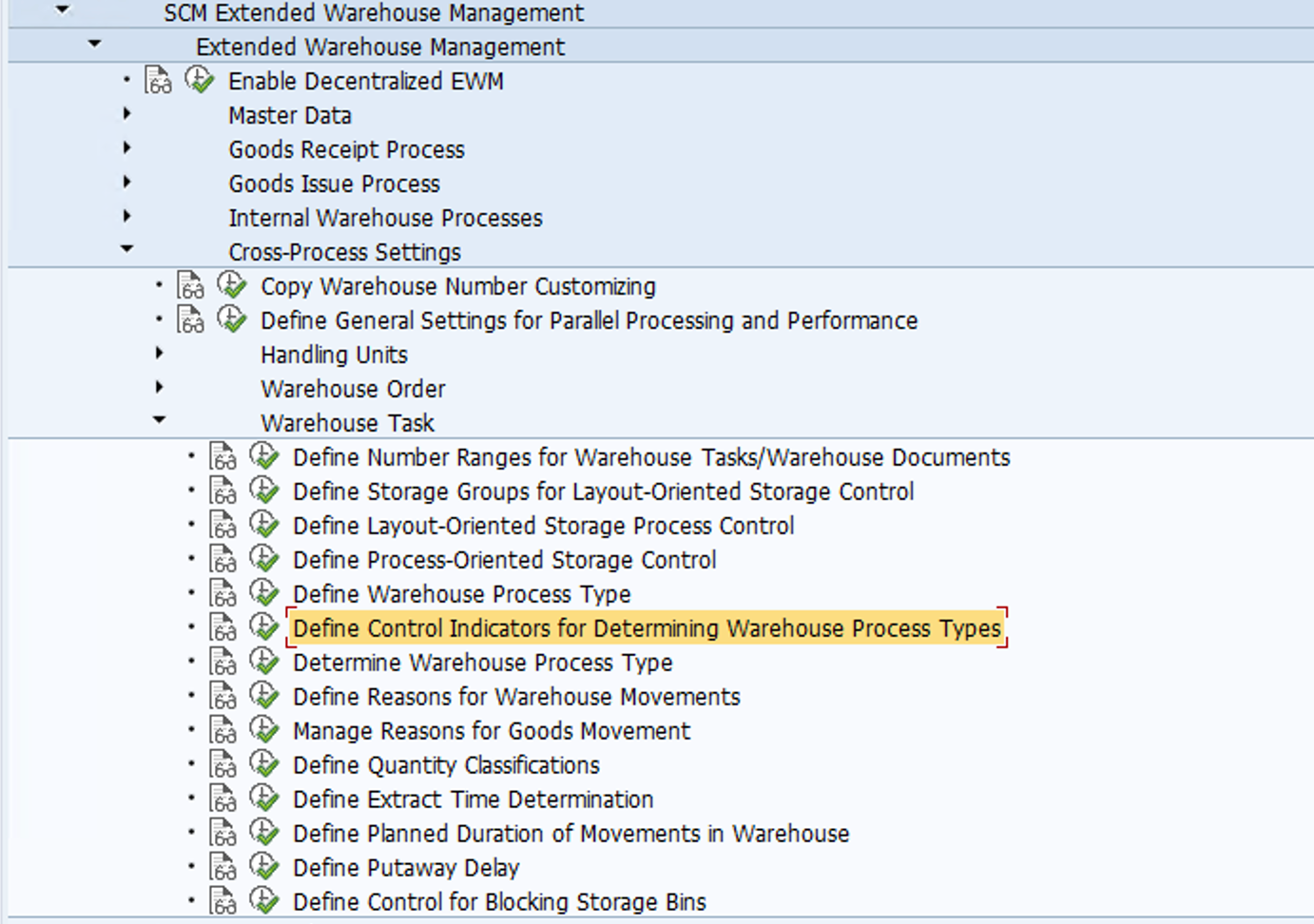
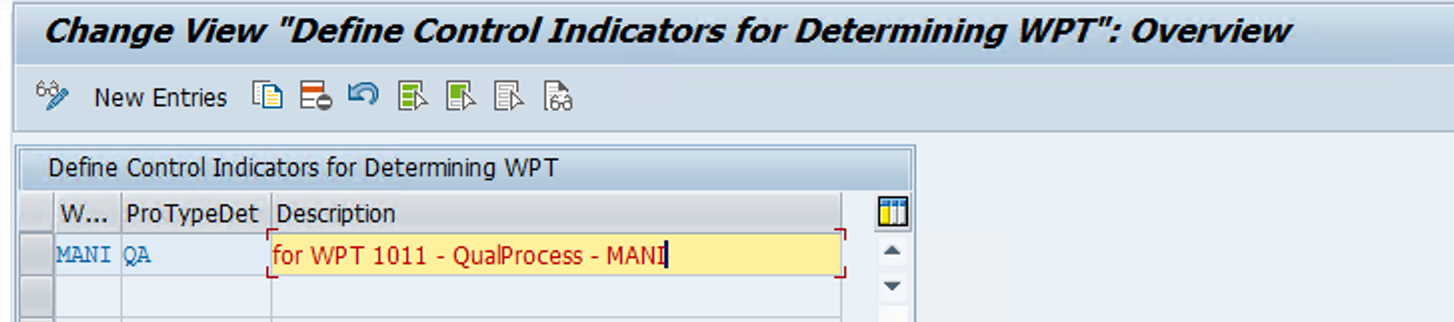
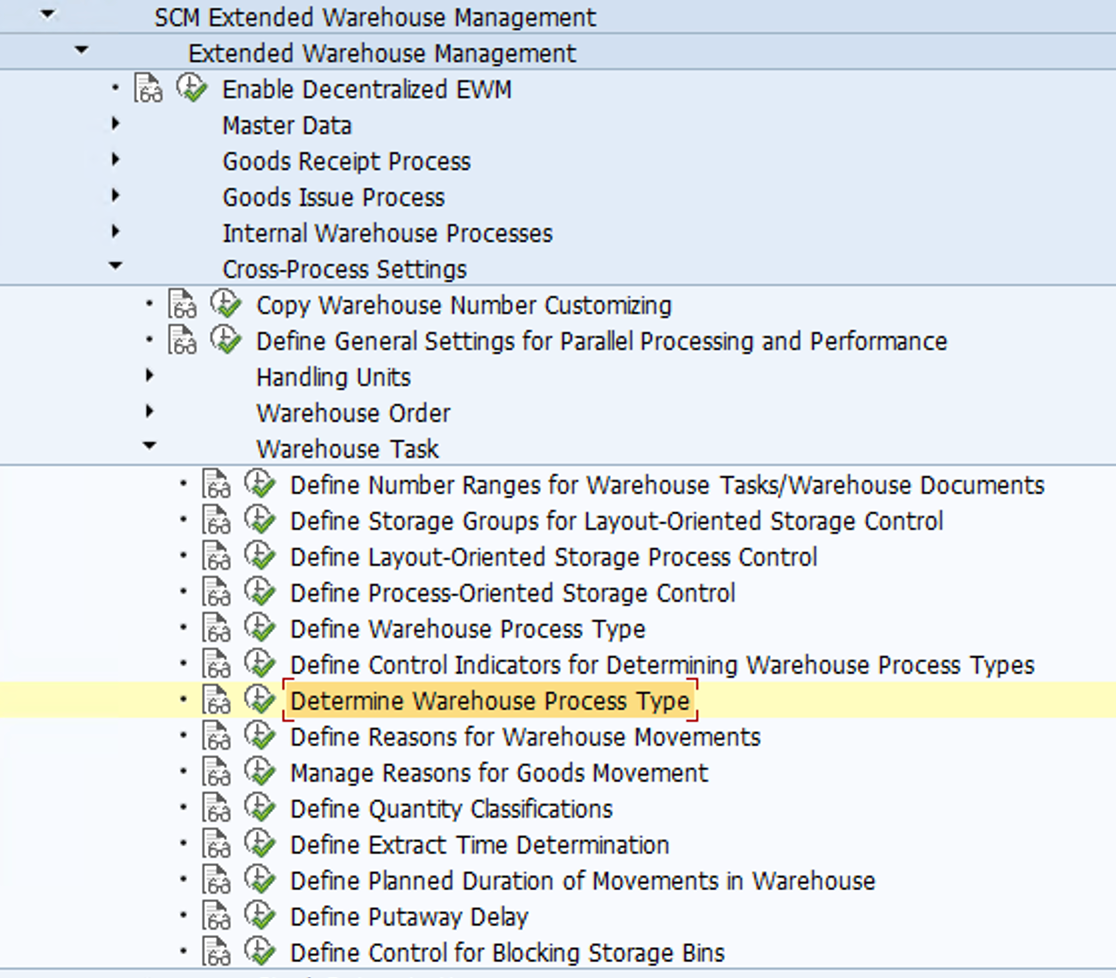
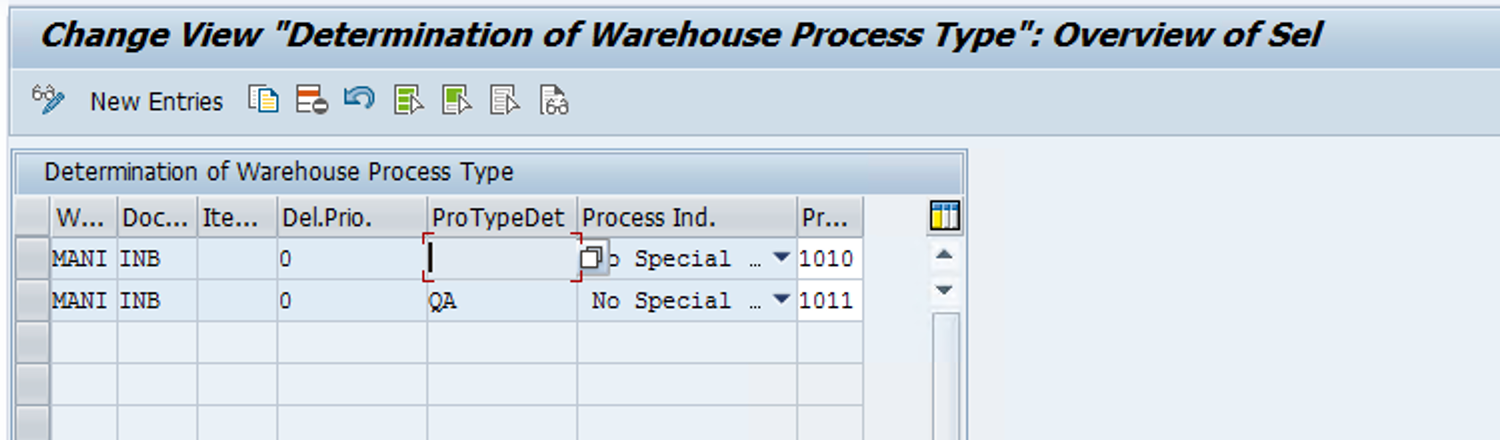
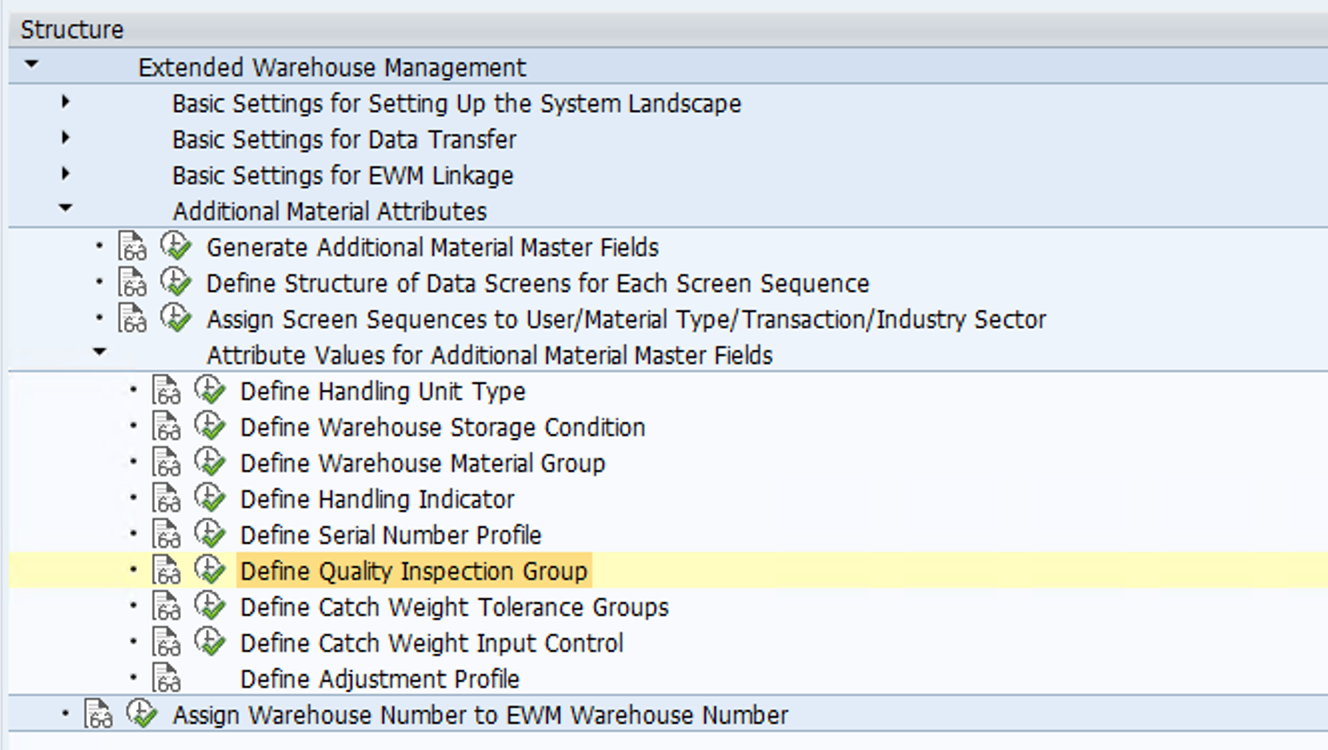
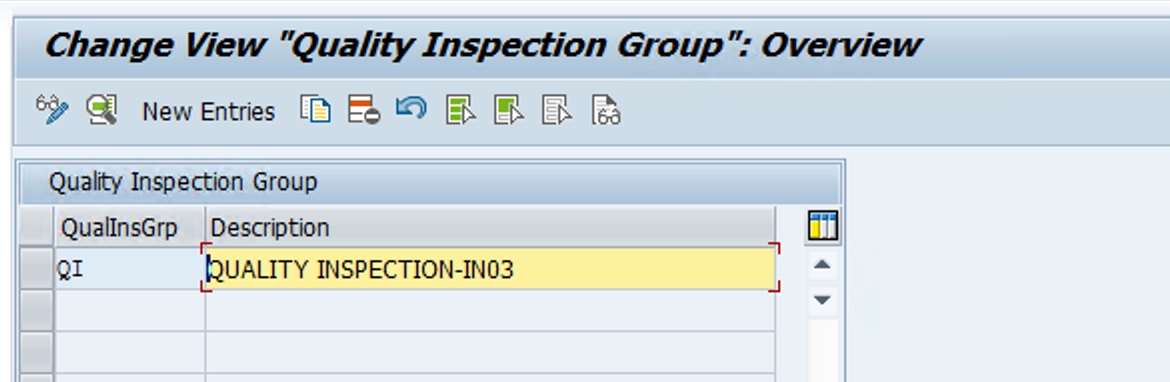
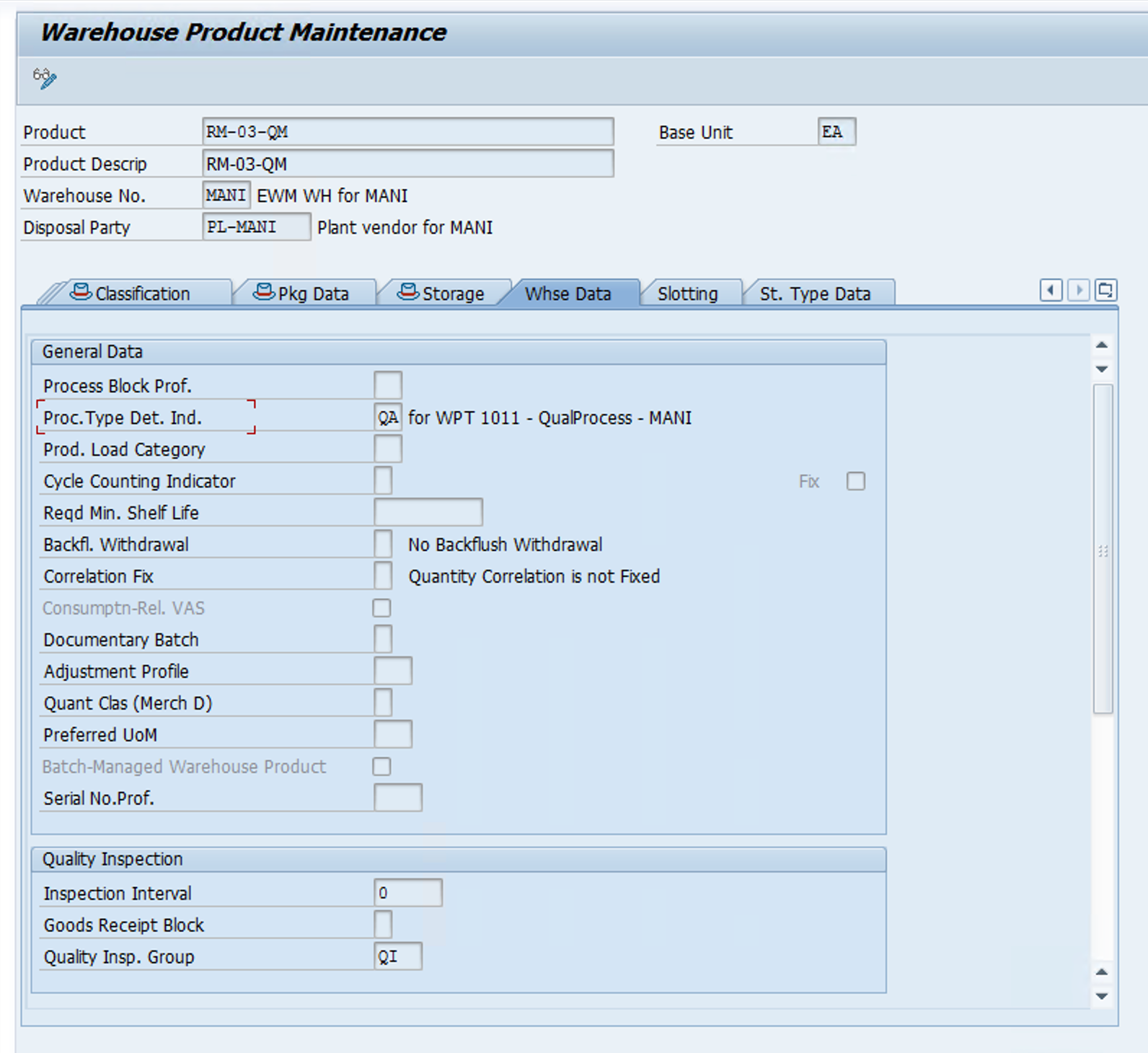
Step 5: Now we need to maintain work center for the quality storage type 8020 where quality inspection will take place.
We need to first define the work center layout and then create work center for our storage type.
Below WCL is copied from a standard layout so that we can use it for our work center configuration.
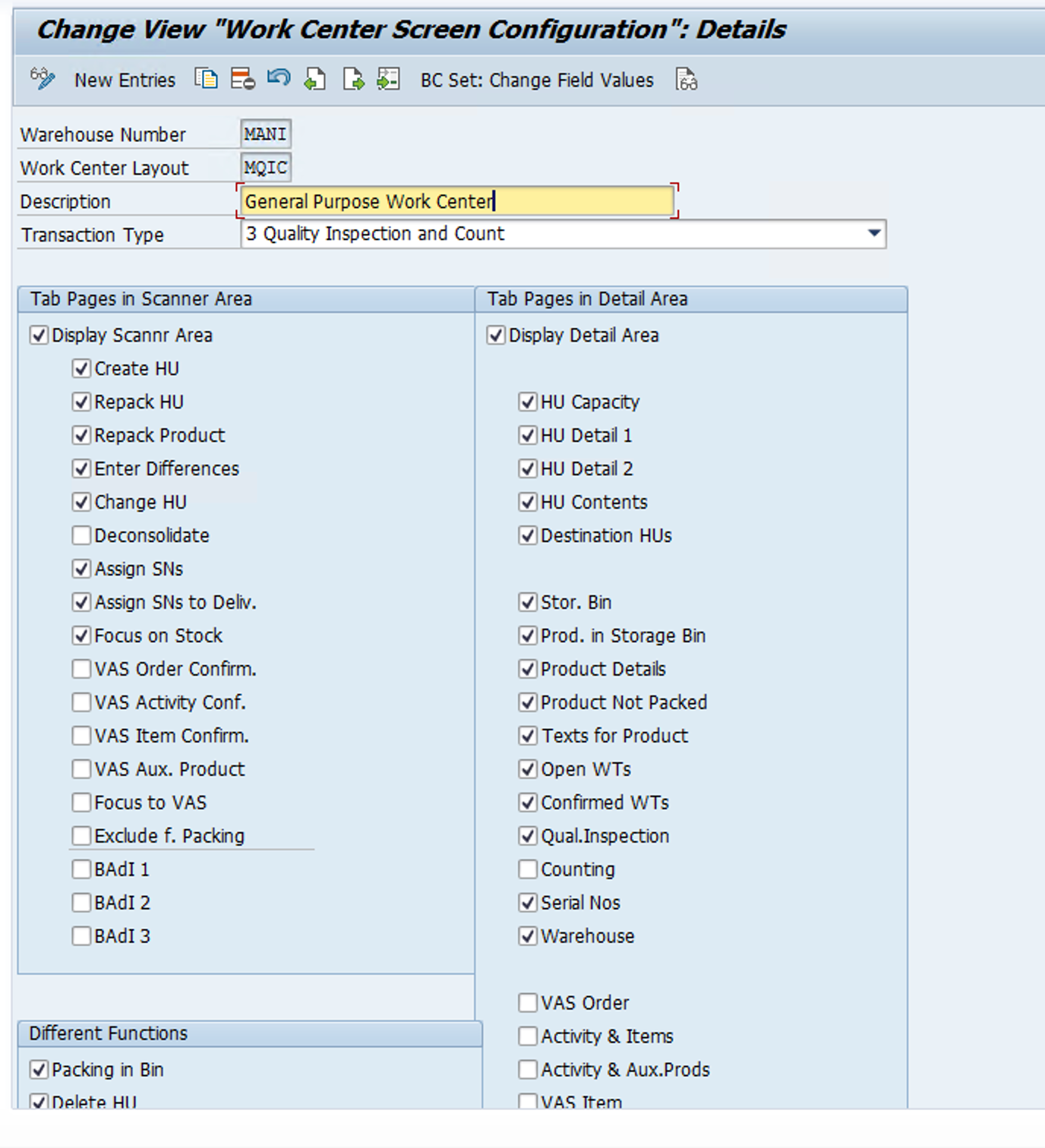
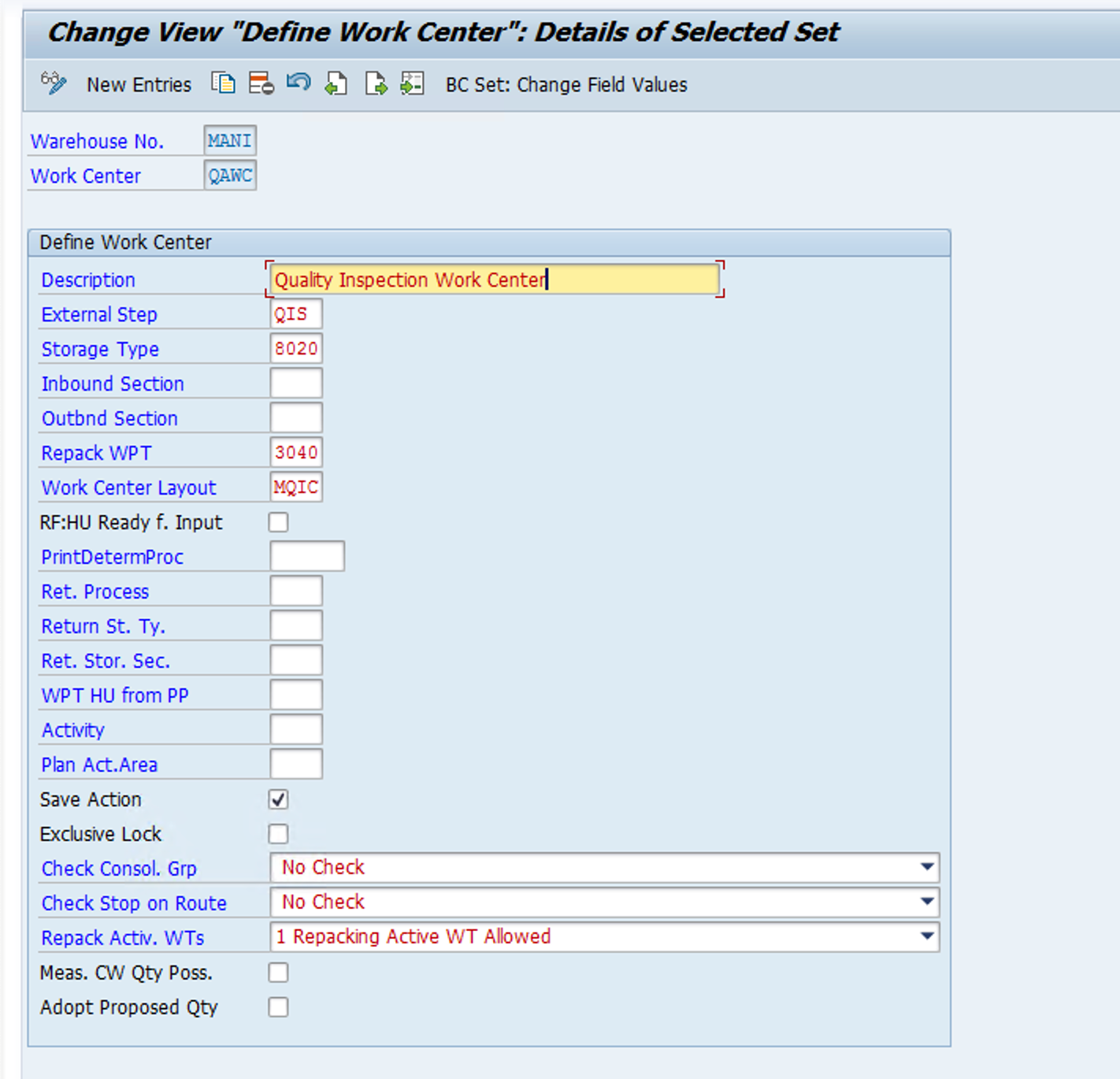
Step 6: Generate and Maintain Inspection Object Types Version. Also define and maintain Warehouse dependent IOTs
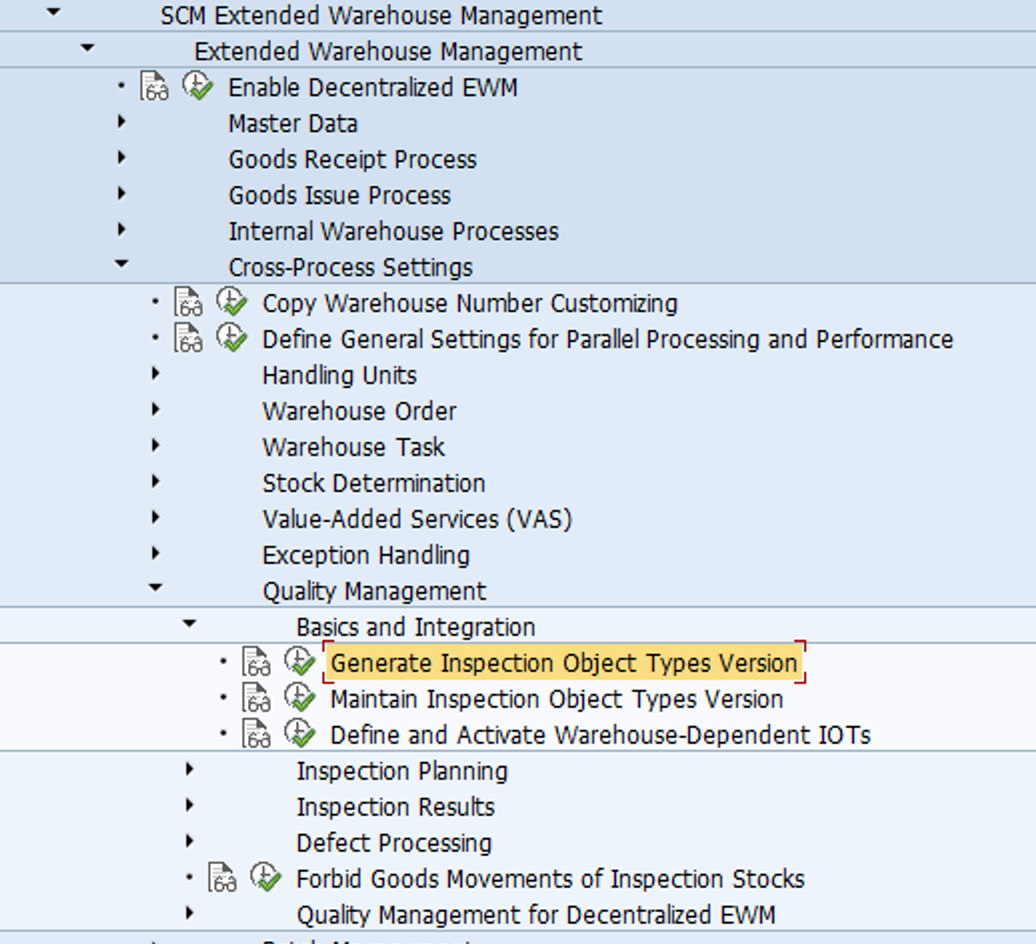
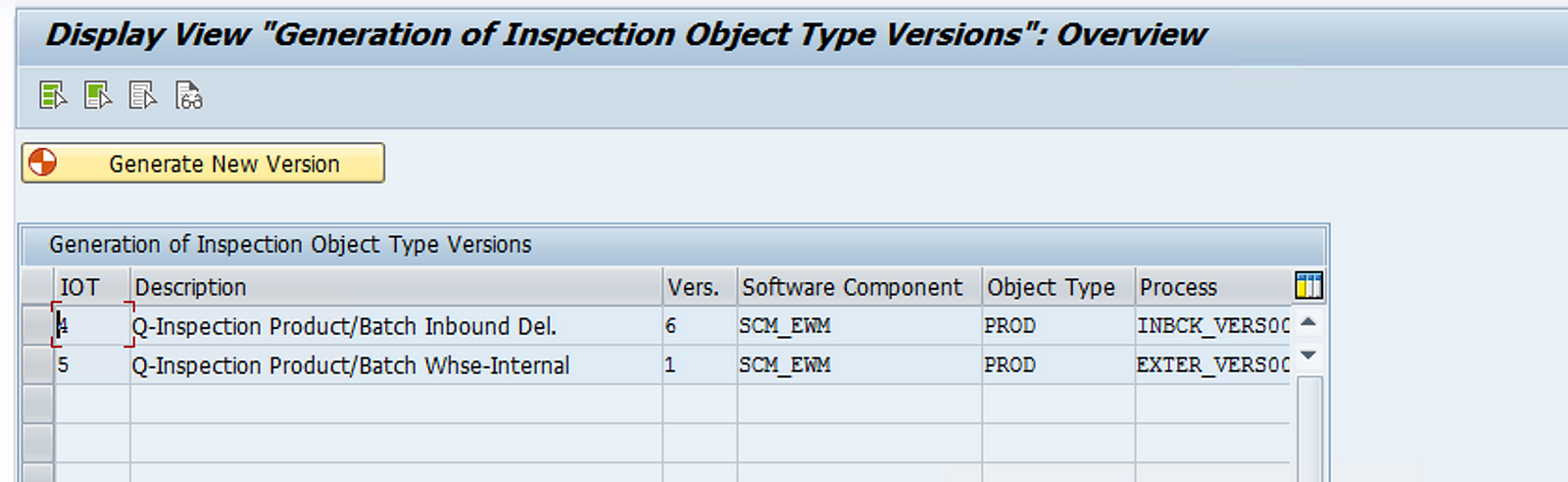
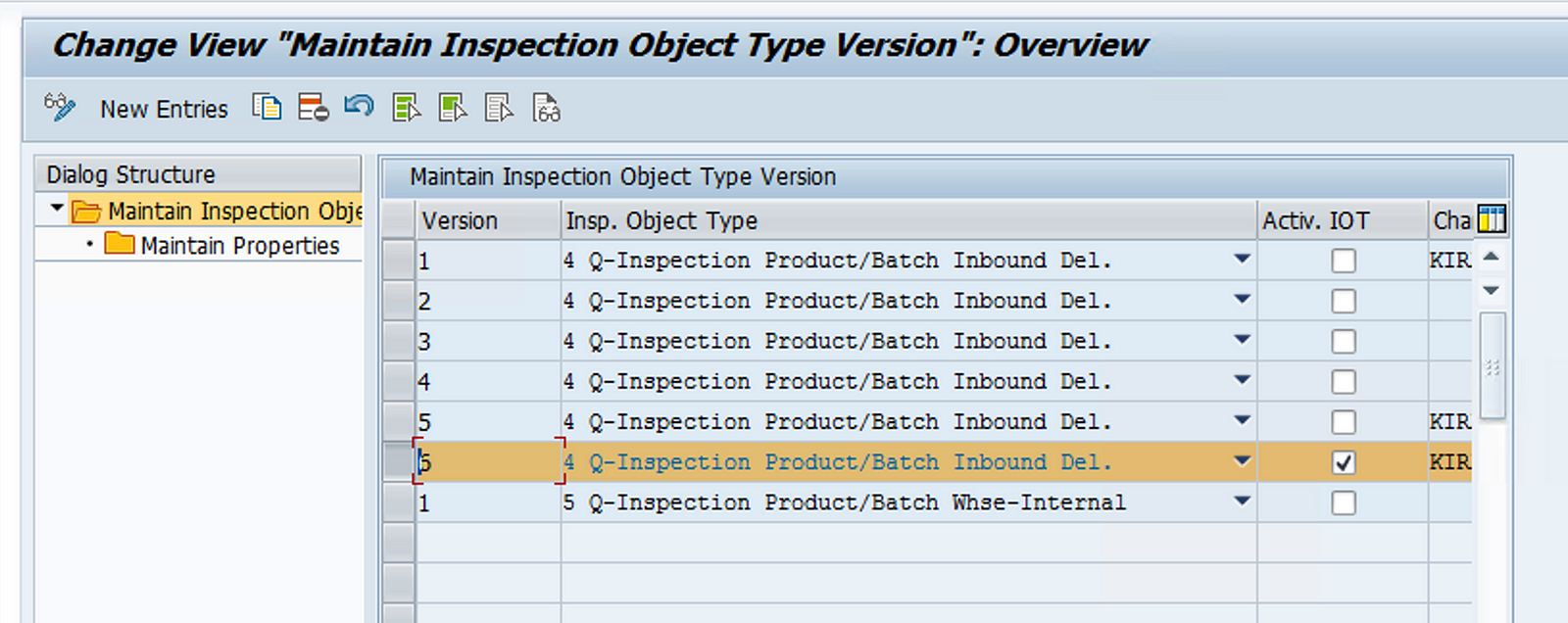
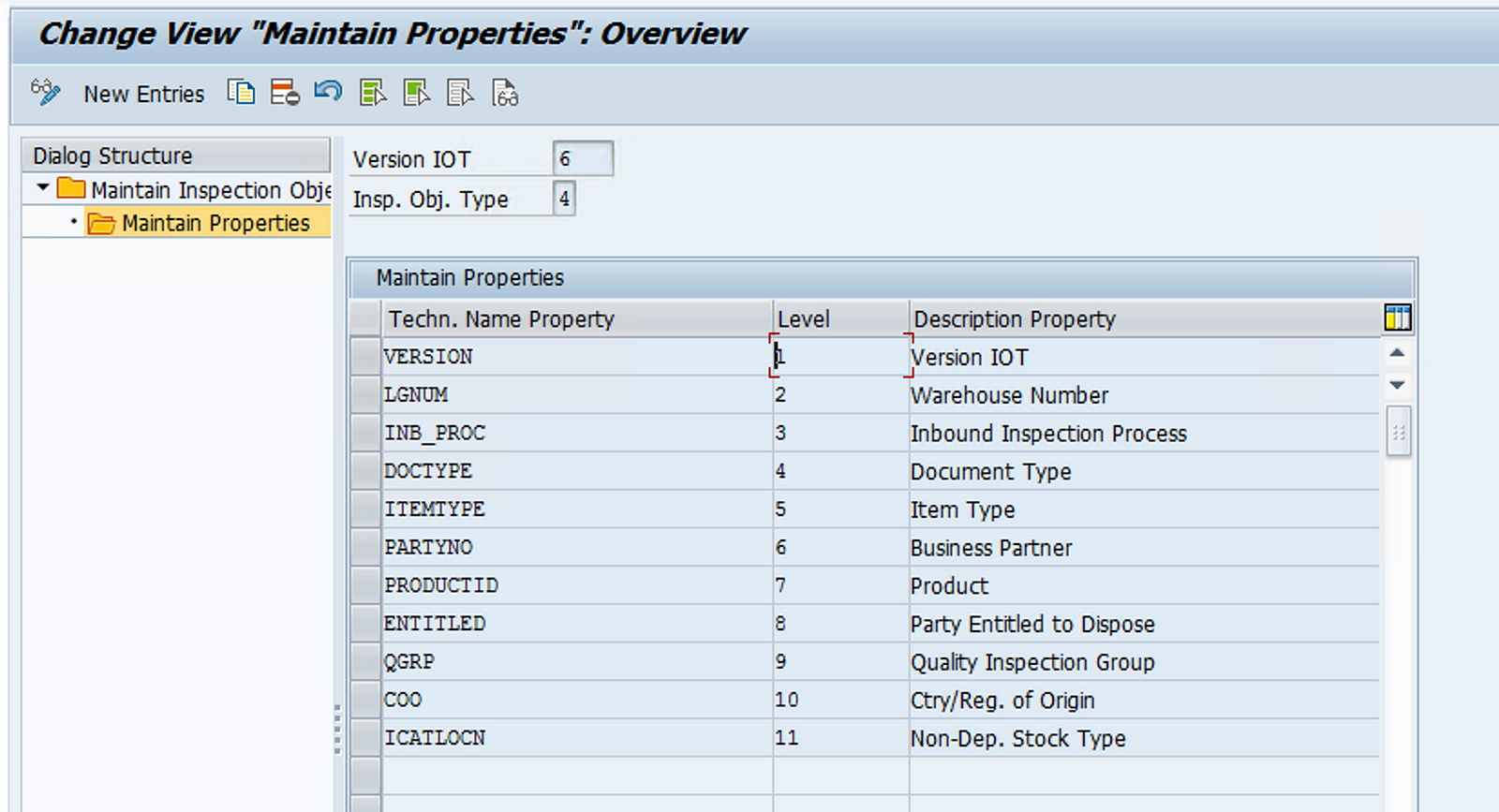
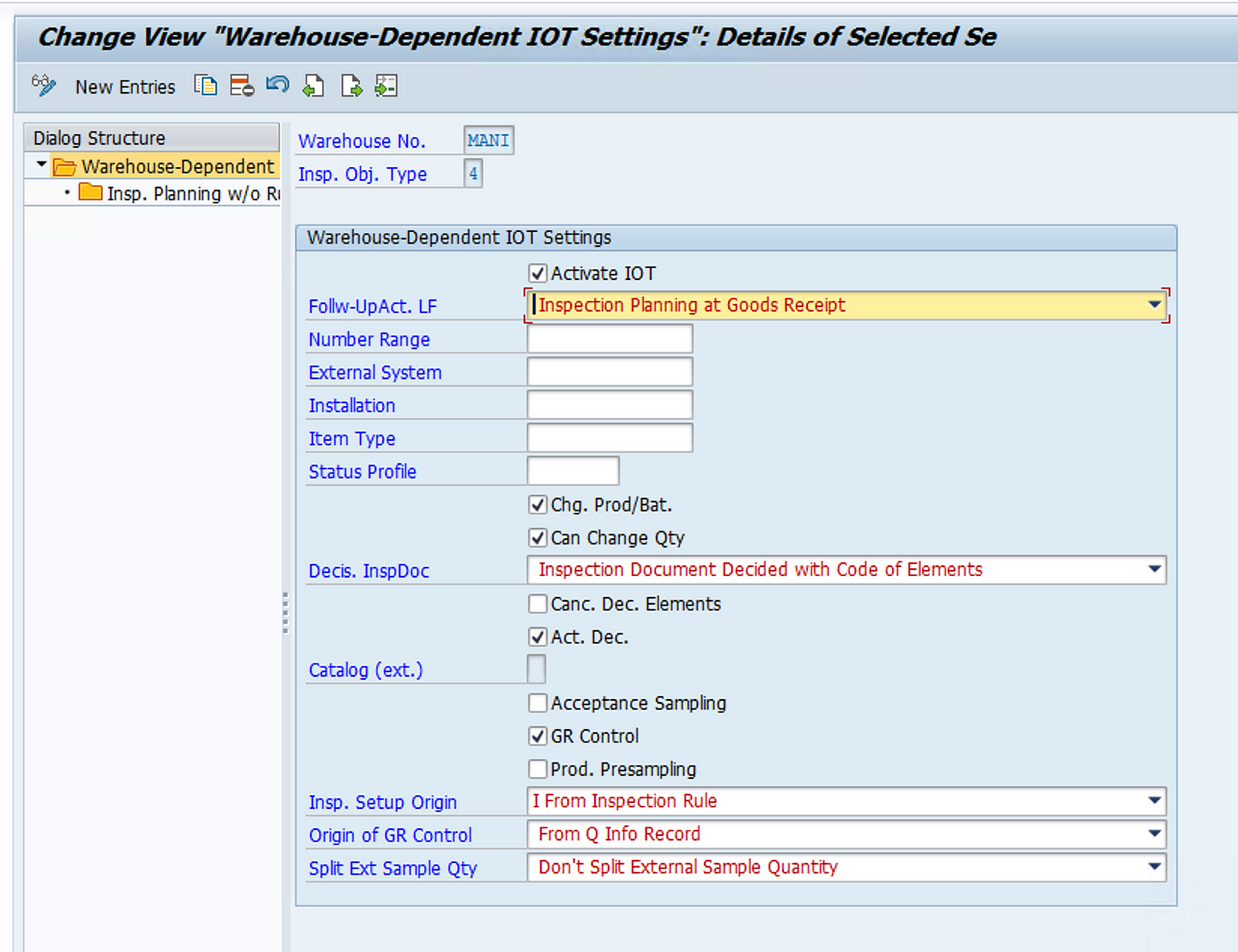
You can define and activate the inspection object types (IOTs) for a warehouse, which help to define the inspection processes to be followed.
If you are using embedded Extended Warehouse Management (EWM) in SAP S/4HANA, you also define settings for the creation of inspection lots for the IOTs used for inspection planning without inspection rules.
If you perform inspection planning with inspection rules, you must generate IOT versions and activate them.
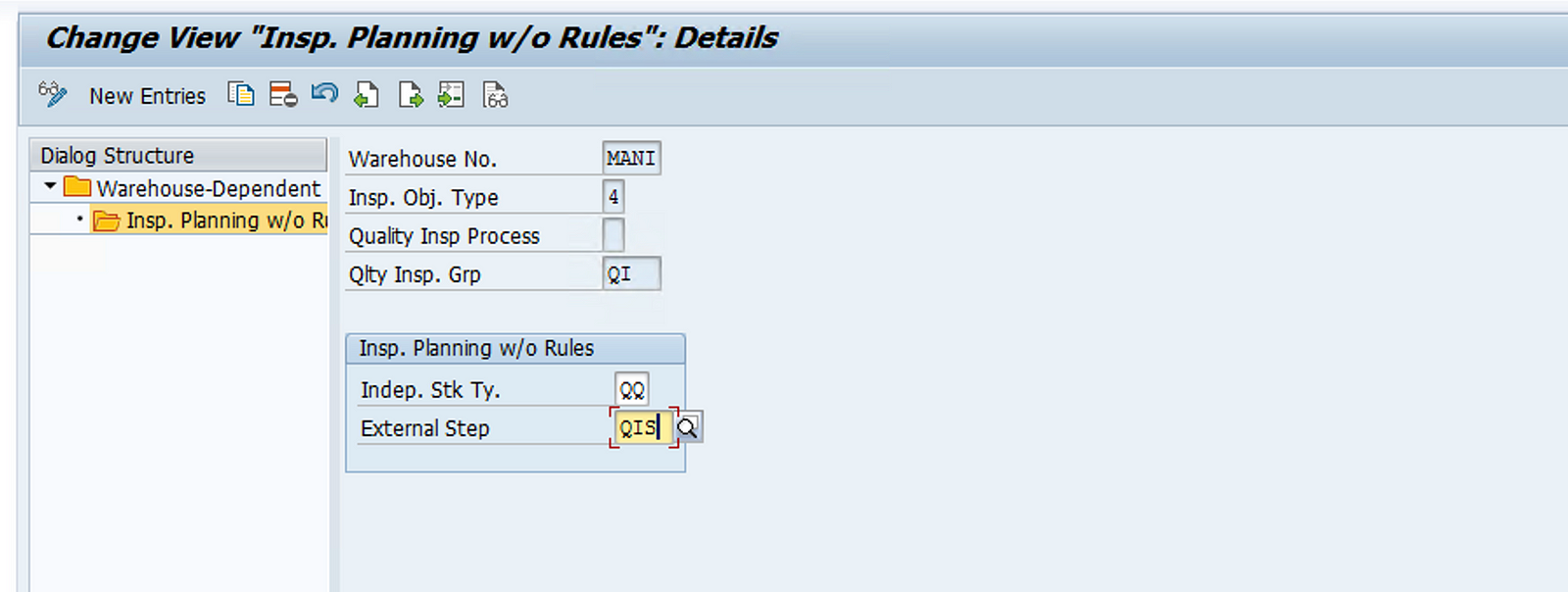
When defining inspection processes for your warehouse, you want to do the following:
>Activate inbound inspections for externally procured goods only
>Perform inspection planning when posting the goods receipt, at the latest
>Control the goods receipt in EWM by the quality info record
>Perform inspection planning without inspection rules
>Activate acceptance sampling
>Be able to change the product or batch and the quantity during the inspection decision process
>Record and save usage decisions and follow-up actions when saving the inspection result
Therefore, you make the following settings:
1. Activate IOT Q-Inspection Product/Batch Inbound Del. (IOT 4) for your warehouse.
2. Specify that you want to perform inspection planning at goods receipt posting.
3. Specify that you can change the product or batch during the inspection decision process.
4. Specify that you can change the quantity during the inspection decision process.
5. Activate acceptance sampling.
6. Activate goods receipt control.
7. Enter No Inspection Rule as the master data used to control inspection planning.
8. Enter From Q Info Record as the master data used to control goods receipt.
9. Specify the settings for inspection planning by choosing Insp. Planning w/o Rules.
Step 7: Now we need to maintain follow up actions in EWM when usage decision will be completed in theS4.
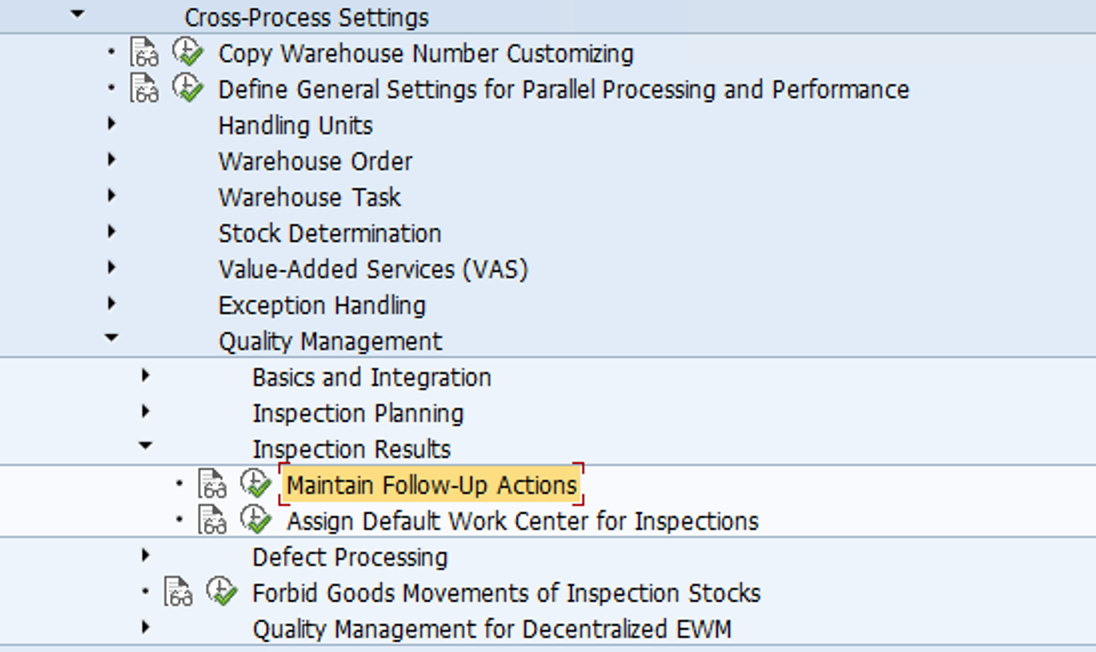
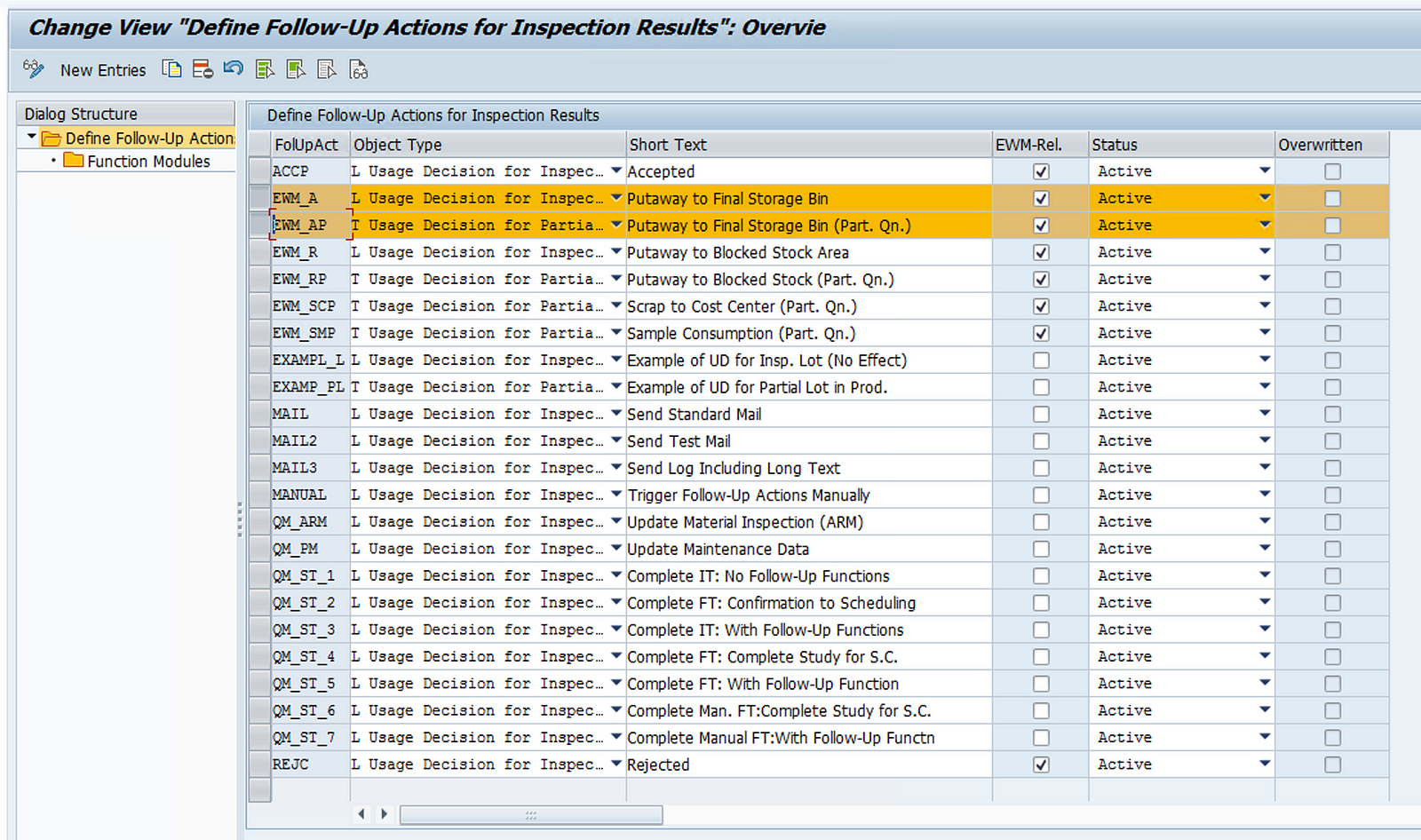
Assign follow up actions to our warehouse number, the stock type will become FF on completion of UD.
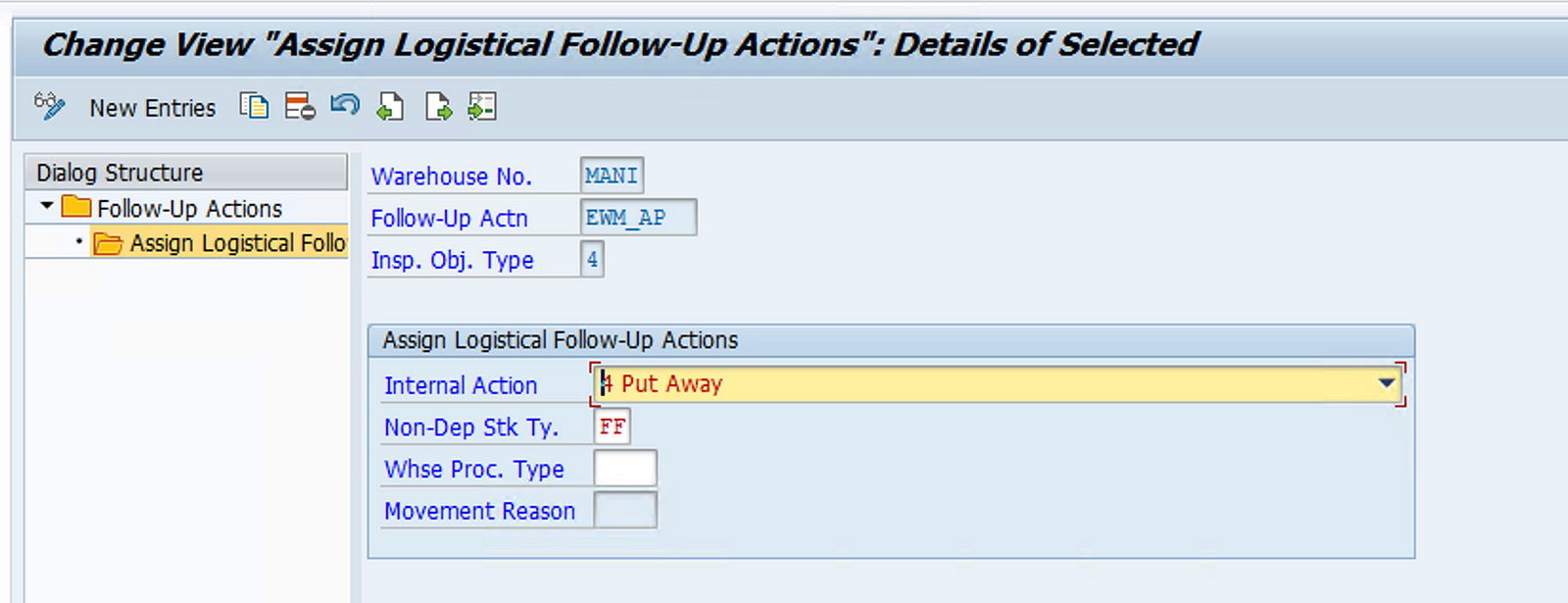
Also assign the default work center for inspection
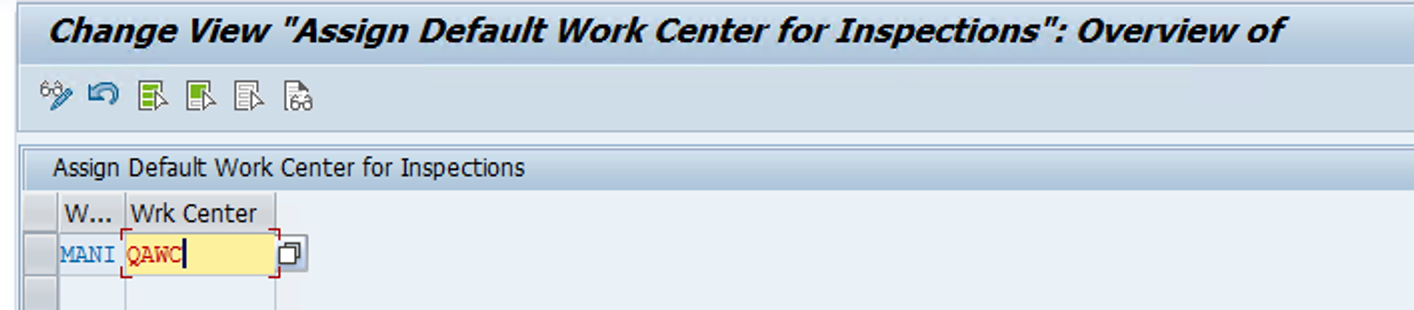
Step 8: Now we need to maintain the inspection rule master data using Tcode : /SCWM/QRSETUP
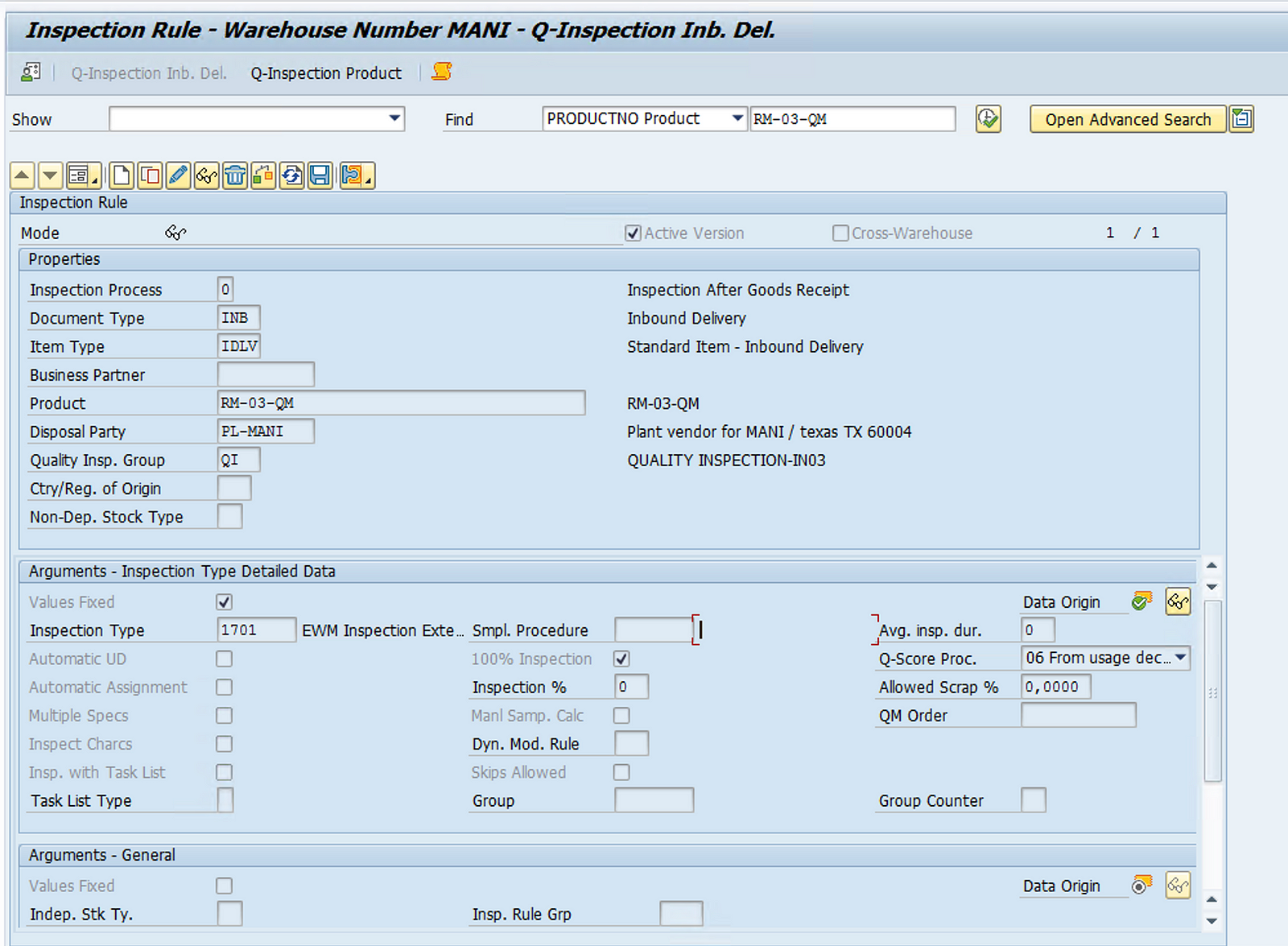
You will also need to setup the EWM putaway search strategy for the Product. Please check this blog for search strategy configuration.
To see the above configuration in action please check this blog.
Please feel free to reach out on LinkedIn if you have any queries or need help with your project.